An important part of caring for a steam locomotive is time-honored boiler wash. Performing boiler washes at regular intervals is mandatory to conform with Federal Railroad Administration regulations and ensures that the locomotive’s boiler is kept free from all corrosion and scaling which would otherwise lead to reduced operating performance and eventually cause damage to the boiler. Boiler washes must be completed after every 31 days the locomotive is in service and is one of the many steps of regular maintenance required to keep a steam locomotive operating. During a wash the boiler is first emptied and then high-volumes of water are flushed through the interior of the boiler and smokebox until no sign of rust, scale or other detritus is detectable in the drainwater.
In order to perform a boiler wash, it is necessary to have numerous access points to the boiler’s interior to direct the water into the boiler as wells as locations for the drainwater to escape. This is achieved through the use of removable plugs of a decent size that can easily be removed and put back in with a steam tight seal. SPEC Machine is reproducing steam era Huron style [Huron Manufacturing, Inc.] couplings and plugs from certified materials for the task.
The couplings will be welded into the boiler shell and the two plugs shown in the above photo (which are actually from the 1385’s old boiler) demonstrate how the plug sits in the coupling and also shows the wide sealing surface that makes the Huron style so easy to use. With a clean thread and sealing surface a gentle tap or two with the heel of your hand on the end of an 18-inch wrench is all that is needed for a perfectly steam-tight fit. Much more force than that will only distort the plug and seat and ruin the sealing surface.
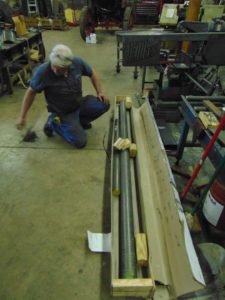
SPEC Machine’s Steve Roudebush opens a shipment of new bronze rods which will soon be formed into washout plugs for 1385’s boiler. Pete Deets photo.
Recently the steam bronze arrived for the new plugs and was photographed being unboxed by SPEC Machine’s Steve Roudebush. Those two sticks total over 300 lbs. of material. The next step is to whittle away anything that doesn’t look like a Huron plug.
Engineering calculations show the threads should be able to withstand pressure up to 13 times greater than the boiler’s design pressure but calculations alone aren’t good enough. One extra coupling was made to serve a dual purpose. First, it will be welded into a piece of test material so we can gauge how badly the heat of the welding process will distort the coupling. The test material will also have a fitting applied to allow the 1385 team to hook it up to the hydrostatic pressure test pump. Once a plug is made, it will be screwed into the coupling and can be pressure tested as a system to further prove the safety of the design before it gets installed on the actual boiler.
Meanwhile in St. Louis, Missouri, Continental Fabricators has continued production work on the new boiler. This photo recently shared by Continental Fabricators’ staff shows the front courses welded together.