In this C&NW #1385 update, we get a glimpse of the process of installing tubes in the boiler.
The tubes are installed by sliding them into the holes on the tubesheet. Their outside diameter is just slightly smaller than the holes in the tube sheet. However, in order to have a water-tight and steam-tight seal, there can’t be any gap. This is achieved through a process called rolling.
In the rolling process the tube is actually expanded from the inside using a roller. The roller presses the end of the tube against the hole in the tubesheet tightly enough to form a steam-tight seal. The end of the tube actually sticks out of the hole a specified amount. The portion that sticks out is then curled outward and back until it touches the tubesheet in a process called beading. If the end of the tube were left hanging out by itself it would soon overheat and burn off or crack. Since the beaded end of the tube is touching the tubesheet it will transfer some of the heat back into the tubesheet and not get hot enough to burn off or crack.
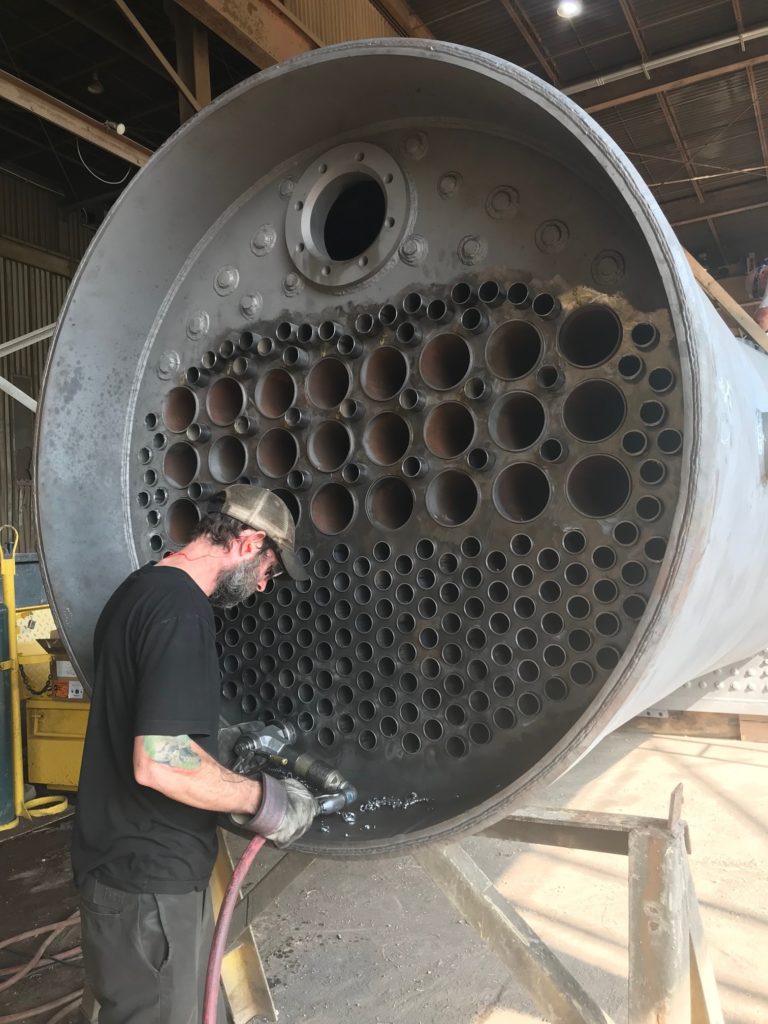
A Continental Fabricators employee trims excess tube material from the front of the boiler. Additional employees are on the firebox-end rolling and beading the tubes. Photos courtesy Continental Fabricators.
Additionally, the arch tubes have now been installed. Arch tubes provide increased firebox heating surface area and allow better circulation of water in the areas surrounding the firebox. The arch tubes also serve to support the brick arch, a series of firebricks that help direct heat from the fire more evenly throughout the firebox.
- Wrappersheet around the firebox showing the stays, arch tube plugs and the external combustion air inlets S. Roudebush photo.
- Detail view of wrappersheet showing the stays, arch tube cleanout holes (with plugs removed) and the external combustion air inlets. S. Roudebush photo.
With the tubes now installed, a countdown clock has begun to tick. A boiler must be disassembled for extensive Federal Railroad Administration mandated inspections every 15 calendar years or 1,472 days of operating – whichever occurs first. Once the first tube was installed, the FRA gives a 1-year grace period in which to complete work before the 15-year time limit begins. If the locomotive is completed in less time, the 15-year clock starts once the FRA accepts the locomotive for service. If the locomotive is not accepted for service within the 1-year grace period, then the 15-year clocks starts anyway.
The next step for C&NW 1385’s boiler is the hydro test. Stay tuned!