Photos and text by Pete Deets
Staybolt Update
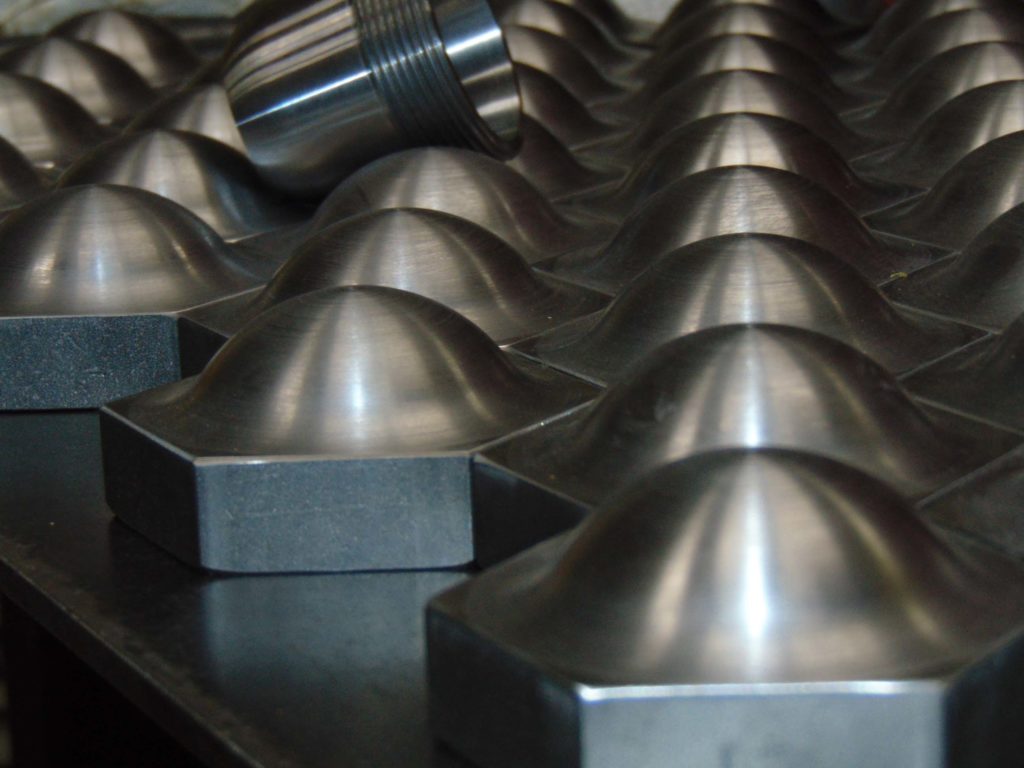
No, this is not a fleet of UFO’s lined up at SPEC Machine. These are the caps for the latest batch of flexible staybolts being made for the 1385.
The caps and sleeves shown (above) and the staybolt itself is completed when a ball end (below left) is threaded onto the bolt and the bolt is placed into the sleeve (below right).
Below is a comparison of the two types.
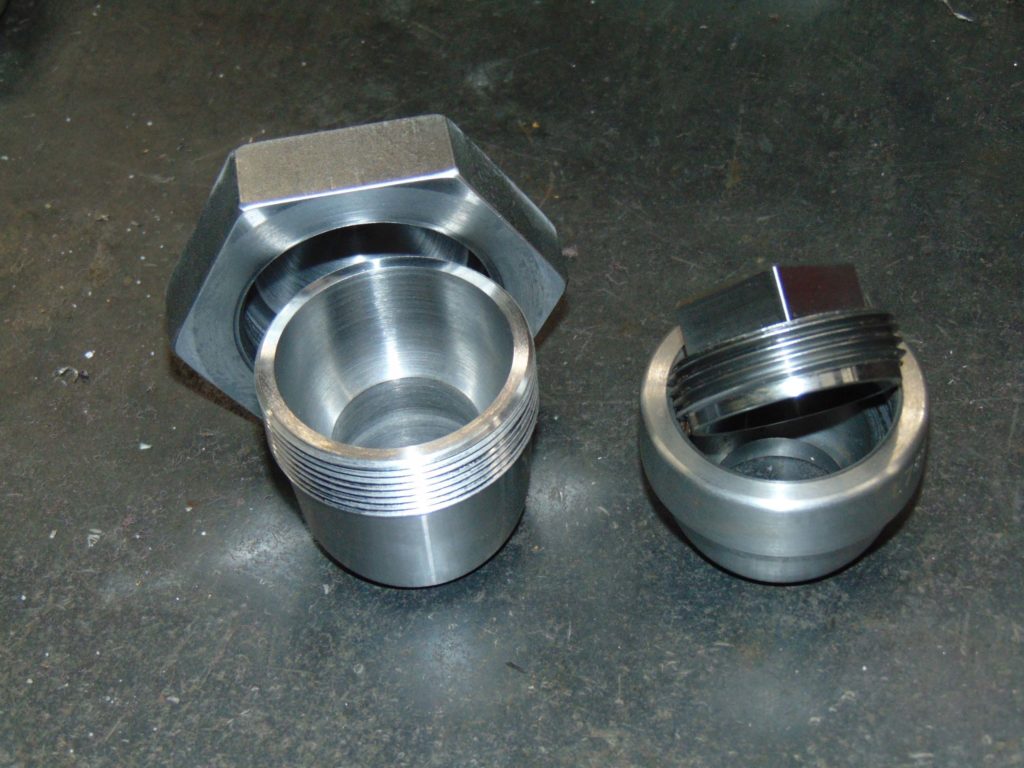
You may wonder why we need 2 types of flexi’s. That is because we have to allow for support of curved as well as flat surfaces. This illustration from the 1938 Flannery Staybolt Catalog shows how the first batch of staybolts will be applied. This is the UW style and is designed to be used where the staybolt will be going through the supported sheet at close to a right angle and the inside and outside sheets are very close to parallel. The flexible staybolts on the throat sheet at the front corners of the firebox will utilize the UW style.
The latest batch is the WR style which is designed to be applied where the inside and outside sheets curve at different rates and do not run parallel. This is the situation near the top of the wrapper sheet and firebox. Because the top of the firebox (the crownsheet) is rolled in a tighter radius than the wrapper sheet and the rigid end of the staybolt needs to be square to the sheet it is attached to the flexible end goes through its’ sheet at some angle.
-
-
UW style flexible staybolt. Illustration from 1938 Flannery Staybolt Catalog.
-
-
WR style flexible staybolt. Illustration from 1938 Flannery Staybolt Catalog.
All these parts are coming together and will be forming a boiler very soon.
A Look Inside the Continental Fabricators Factory
I took a quick trip with Steve & Tyler Roudebush of SPEC Machine to deliver a palette of parts to Continental Fabricating in St. Louis as well as inspect the progress on the new boiler for 1385. More photos and details about the boiler will be posted later but I wanted to share a few shots of Continental’s shop. I hope this will give folks a feel for the size of operation building our vessel.
-
-
Continental keeps on hand over a million pounds of certified material stocks.
-
-
A few pieces in process.
-
-
This plate roller is designed to shape steel plates 6 inches thick. It will accept a flat plate and roll it into a round barrel shape.
-
-
Radial arm drill. Look closely and you’ll see a worker inside the vessel that’s sitting on the radial arm drill.
-
-
The 20 x 20 x 80 ft heat treat oven.
-
-
A small vertical lathe.
-
-
Steve, Tyler of SPEC Machine and Tom G. of Continentral.
-
-
Some slightly larger machines.
-
-
Incoming material including the steam dome cover for the 1385. Also a small shear and press in the background.
-
-
A slightly larger press.