This is an older update that was delayed getting posted online. Thank you for your patience. — The Webmaster
Adding Cistern Piping
In October, volunteers continued working on Chicago & North Western #1385’s tender cistern ports. This included installing bottom fill piping and ports for connecting to a canteen car, otherwise known as an auxiliary tender.
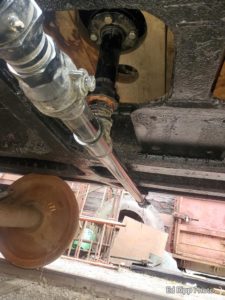
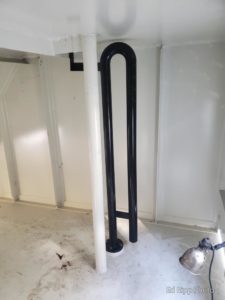
On Mid-Continent’s shortline railway, 1385’s tender has more than enough water capacity to keep 1385 steaming, but a canteen car becomes more important when water sources are harder to come by. Mid-Continent’s canteen car, which offers an additional 12,000 gallons of water capacity, was frequently found trailing 1385’s tender when the locomotive was venturing around the Upper Midwest on mainline excursions. Mid-Continent’s canteen car is currently on display near the museum’s water tower.
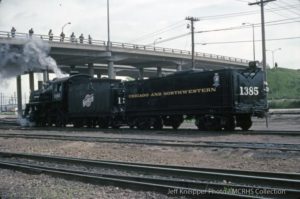
Test Filling the Tender
On October 29th, a team of volunteers including Pete Deets, Kyle Gerke, Richard Gruber, and Ed Ripp filled 1385’s tender with water up to its maximum capacity. This was done for testing purposes.
Although the Mid-Continent’s Engine House has a faucet connected to the museum’s groundwater well, that system lacks sufficient capacity to fill a tender in a timely fashion. For a quicker fill time, volunteers utilized a submersible pump that had last been used when steam was in regular service, and pumped the water directly out of the adjacent Baraboo River using a 2-inch hose. The river water contains many impurities and will not be used when running steam in the future, but for doing a test fill of the tender, Baraboo River water would work just fine.
Attached to the hose was a water meter to allow an accurate measurement of the gallons pumped into the tender. While filling the tank, one person watched the water meter and another person was on top of the tender marking a board with measurement lines. This was necessary because 1385’s tender has a new cistern. These measurements will be transcribed to a water level meter used by engine crews in the future.
Measurements were also taken of the drawbar pocket and the center of the rear coupler when the tender was empty and again when full. Marks were also made on each truck at the bolster and pedestal jaw at empty, half-full, and full to see how much the springs settled with the differing weights.
During this testing, some additional to-do items were discovered and added to the work list.
Upcoming Work
Volunteers kept busy preparing for and hosting Santa Express in November and December no additional work sessions on the 1385’s tender were held in 2022, but in December the tender was moved inside the Engine House to permit work to continue during the winter months. The first winter work session inside the Engine House is tentatively scheduled for January 7th and 8th. Volunteers may also be working on Western Coal & Coke #1 and performing some general shop cleanup/organization work.
Persons interested in volunteering for this or future volunteer sessions should contact Ed Ripp, General Foreman of Steam Power, or fill out the volunteering inquiry form.